How Slitting and Rewinding Enhances Tissue Paper Manufacturing?
Tissue paper is a soft and absorbent paper product that has various uses for personal hygiene, household cleaning, and industrial applications. It is made from wood pulp or recycled paper through a series of processes, such as pulping, refining, forming, drying, creping, and calendering. These processes produce a large roll of tissue paper, called a parent roll, that can weigh up to several tons and have a diameter of up to 3 meters.
However, the parent roll is not the final tissue product. It needs to undergo another process called slitting and rewinding, which cuts the parent roll into smaller rolls of desired width and diameter, and rewinds them onto cardboard cores. The slitting and rewinding process is a vital step in the tissue paper production system, as it offers several benefits for the tissue paper manufacturers and customers. And below are the key benefits of the slitting and rewinding process in detail.
Customization of Tissue Products
The slitting and rewinding process allows customization of tissue products by width, diameter, quality parameters. Different tissue products require different dimensions and specifications, such as basis weight, tensile strength, softness, bulkiness, etc. By slitting and rewinding the tissue parent roll, the tissue paper manufacturers can produce different product variations from the same parent roll. For example, a parent roll with a width of 2.8 meters can be slit into four rolls with a width of 0.7 meters each, or two rolls with a width of 1.4 meters each. Similarly, a tissue mother roll with a diameter of 2.5 meters can be rewound into smaller rolls with diameters ranging from 0.9 to 1.8 meters. The slitting and rewinding process also enables the adjustment of quality parameters such as basis weight and caliper by changing the winding tension and nip pressure.
Product Diversity
The slitting and rewinding process enables production of different product variations from the same tissue paper parent roll. This means that the tissue paper manufacturers can offer a wide range of tissue products to their customers without having to produce multiple tissue parent reels with different specifications. This reduces the production costs and increases the product diversity for the tissue paper manufacturers.
Customer Satisfaction
The slitting and rewinding process facilitates meeting specific customer requirements for tissue products. Different customers may have different preferences and needs for tissue products, such as color, pattern, embossing, perforation, etc. By slitting and rewinding the parent roll, the tissue paper manufacturers can customize their tissue products according to the customer’s specifications. For example, a customer may request a tissue product with a specific color or pattern that is not available in the parent roll. The tissue paper manufacturer can then apply the color or pattern to the smaller rolls after slitting and rewinding the tissue master roll. Similarly, a customer may request a tissue product with a specific embossing or perforation that is not available in the parent roll. The tissue paper manufacturer can then apply the embossing or perforation to the smaller rolls after slitting and rewinding the tissue master roll.
Production Flexibility
The slitting and rewinding process provides flexibility to adjust production per market demand. The market demand for tissue products may vary depending on various factors such as seasonality, consumer behavior, economic conditions, etc. By slitting and rewinding the tissue master roll, the tissue paper manufacturers can adapt their production to meet the changing market demand. For example, if there is an increase in demand for toilet paper due to a pandemic outbreak or a natural disaster, the tissue paper manufacturer can slit and rewind more parent rolls into toilet paper rolls than other tissue products. Similarly, if there is a decrease in demand for facial tissues due to a change in consumer preference or a competitive pressure, the tissue paper manufacturer can slit and rewind less parent rolls into facial tissue rolls than other tissue products.
Material Savings
The slitting and rewinding process results in material savings compared to sheets cut from large parent rolls. Some tissue products are produced by cutting sheets from large parent rolls instead of slitting and rewinding them into smaller rolls. However, this method results in more material waste due to trim losses at the edges of the sheets. By slitting and rewinding the tissue paper mother roll into smaller rolls with precise widths and diameters, the tissue paper manufacturers can reduce material waste and save costs.
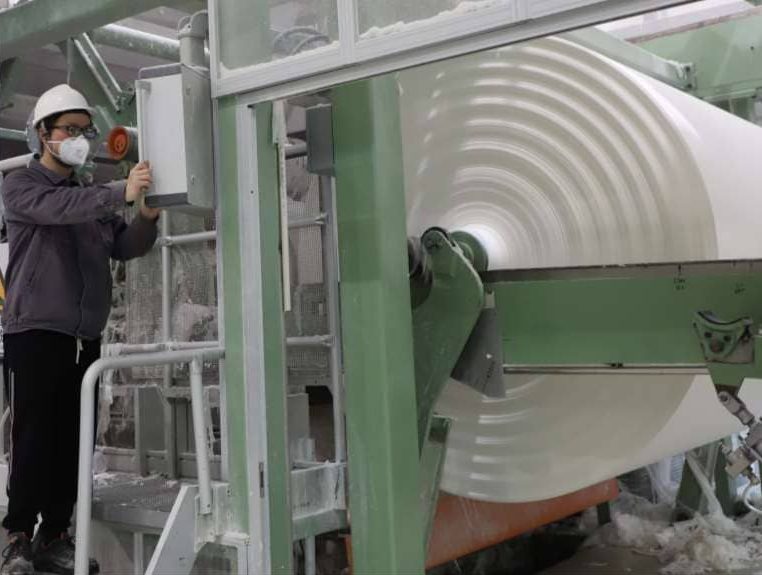
Efficiency Improvement
The slitting and rewinding process improves efficiency of downstream converting processes. The downstream converting processes involve further processing of the smaller rolls into final tissue products by adding features such as folding, cutting, packaging, etc. By slitting and rewinding the tissue base roll into smaller rolls with optimal dimensions and quality parameters, the tissue paper manufacturers can improve the efficiency and performance of the downstream converting processes. For example, smaller rolls with uniform diameter and tension can reduce the risk of web breaks and wrinkles during the folding and cutting processes. Smaller rolls with consistent quality and specifications can also reduce the need for quality checks and adjustments during the packaging process.
Operation Independence
The slitting and rewinding process allows independent operation of upstream paper making and downstream converting. The upstream paper making process involves producing the tissue base roll from wood pulp or recycled paper. The downstream converting process involves producing the final tissue products from the smaller rolls. By slitting and rewinding the parent roll into smaller rolls, the tissue paper manufacturers can decouple the upstream paper making and downstream converting processes. This means that the upstream paper making process can operate at a constant speed and capacity, regardless of the variations in the downstream converting process. This also means that the downstream converting process can operate at a variable speed and capacity, depending on the market demand and customer requirements. This allows the tissue paper manufacturers to optimize their production system and increase their profitability.
Modular Expansion
The slitting and rewinding process enables modular expansion of production capacity. The production capacity of tissue paper is determined by the size and number of parent rolls that can be produced by the paper machine. However, increasing the production capacity of parent rolls may require significant capital investment and technical challenges for the tissue paper manufacturers. By slitting and rewinding the parent roll into smaller rolls, the tissue paper manufacturers can increase their production capacity of final tissue products without increasing their production capacity of parent rolls. This is because they can add more slitting and rewinding machines to their production system, which are relatively cheaper and easier to install than paper machines. This allows the tissue paper manufacturers to expand their production capacity in a modular and flexible way.
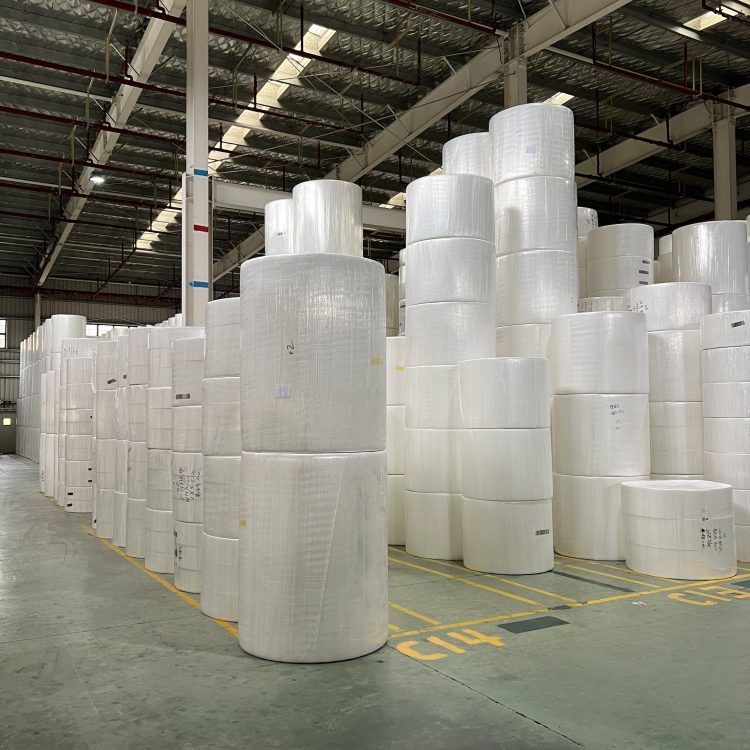
Warehousing Reduction
The slitting and rewinding process reduces warehousing needs for large parent rolls. Large parent rolls require more storage space than smaller rolls due to their size and weight. By slitting and rewinding the tissue parent reel into smaller rolls, the tissue paper manufacturers can reduce their warehousing needs for large parent rolls. This saves them storage costs and space.
Quality Control
The slitting and rewinding process facilitates quality control procedures after paper making. The quality of tissue paper is affected by various factors such as raw material, additives, chemicals, temperature, humidity, etc. By slitting and rewinding the parent roll into smaller rolls, the tissue paper manufacturers can perform quality control procedures after paper making to ensure that their tissue products meet the desired standards. For example, they can measure and adjust the basis weight, tensile strength, softness, bulkiness, etc of the smaller rolls after slitting and rewinding them from the tissue paper parent reel. They can also detect and remove any defects or impurities that may have occurred during paper making or slitting and rewinding processes.
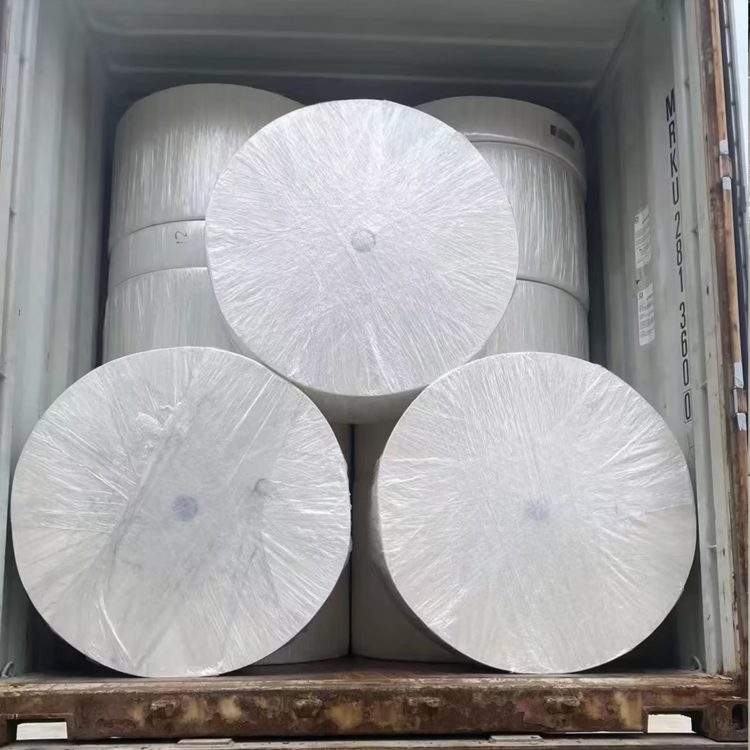
Transportation Costs
The slitting and rewinding process lowers transportation costs due to smaller rolls. Smaller rolls are easier to transport than large tissue parent rolls due to their size and weight. By slitting and rewinding the tissue parent roll into smaller rolls, the tissue paper manufacturers can lower their transportation costs for delivering their tissue products to their customers or distributors. This also reduces their environmental impact due to lower fuel consumption and carbon emissions.
Conclusion
The slitting and rewinding process is a vital step in the tissue paper production system that provides several benefits for the tissue paper manufacturers and customers. It allows customization of tissue products by width, diameter, quality parameters; enables production of different product variations from same parent roll; facilitates meeting specific customer requirements for tissue products; provides flexibility to adjust production per market demand; results in material savings compared to sheets cut from large parent rolls of tissue paper; improves efficiency of downstream converting processes; allows independent operation of upstream paper making and downstream converting; enables modular expansion of production capacity; reduces warehousing needs for large parent rolls; facilitates quality control procedures after paper making; lowers transportation costs due to smaller rolls. The slitting and rewinding process unlocks flexibility and customization in tissue product manufacturing. It is a critical step that enables efficient tissue paper production system.