The Relationship Between Pulping Technology and Tissue Paper Quality
The quality of tissue paper is closely related to various stages of the production process, and pulping, as one of the core technologies in paper manufacturing, plays a decisive role in the final performance of the paper. By adjusting the degree of pulping and process parameters, key properties of tissue paper, such as strength, softness, and absorbency, can be effectively improved. Below is an expanded explanation of how pulping technology influences the quality of tissue paper from various perspectives.
1. Increasing Filler Retention: The Relationship Between Ash Content and Pulping Degree
In tissue paper production, when the ash content is too low, it often leads to a decrease in filler retention. In this case, increasing the pulping degree can close the pore structure of the paper sheet, allowing the filler to be better retained within the pulp. This improves the strength and uniformity of the paper. This adjustment is particularly crucial for tissue paper with high filler content.
2. Preventing Sheet Floating on the Cylinder: Enhancing Adhesion Between Paper and Cylinder
In tissue paper production, if the paper sheet floats on the drying cylinder, it is often due to insufficient adhesion between the sheet and the cylinder. To solve this issue, the pulping degree can be increased to enhance the compactness of the paper sheet, thereby improving its adhesion to the cylinder and ensuring stable production.
3. Adhesion to Drying Cylinder: Optimizing Paper Structure by Adjusting Pulping Degree
When the paper sheet adheres to the drying cylinder, it may be because the pulp contains too many fine fibers, making the paper structure too tight. In this case, reducing the pulping degree allows for a more even fiber distribution, improving the paper’s air permeability and flexibility, thus avoiding adhesion problems.
4. Freeness and Paper Defects: Maintaining Appropriate Pulping Degree
During tissue paper production, excessive freeness of the pulp may cause issues such as sheet floating and creases. If other process parameters are within the required range, ensuring sufficient refining degree during pulping is essential to prevent these defects and maintain the flatness and uniformity of the paper sheet.
5. Waste Paper Spots and Pulping Equipment Compatibility
If waste paper spots occur during pulping, it is often because the fibers in the repulper are not sufficiently disintegrated. In this case, increasing the capacity of the repulper and possibly using slush pulping can help. If a pulping machine is used as a disintegrator, it may not achieve the desired effect. Therefore, selecting the right pulping equipment and processes is crucial.
6. Bulk and Pulping Degree: Maintaining the Softness of the Paper
Bulk is an important indicator of tissue paper’s softness. A high pulping degree makes the paper structure too compact, reducing its softness. Therefore, to increase the bulk and comfort of tissue paper, the pulping degree should be reduced, allowing for a more open paper structure.
7. Improving Burst Strength: The Impact of Pulping Degree
The burst strength of tissue paper is closely related to its overall strength. By adjusting the pulping degree, the fiber bonding strength can be significantly enhanced, thereby improving the paper’s resistance to breakage. This is particularly important when producing high-strength tissue paper.
8. Calendering Black Spots and Pulping Uniformity
If black spots or blemishes appear on the surface of tissue paper during calendering, it may be due to poor formation. The uniform distribution of fibers during the pulping process directly affects how evenly the pulp is spread on the wire. By optimizing pulping techniques, the paper’s formation quality can be improved, preventing such defects.
9. Thickness and Pulping Degree: An Inverse Relationship
The thickness of tissue paper is generally inversely proportional to the pulping degree. As pulping progresses, the fibers become finer, leading to a noticeable reduction in paper thickness. Therefore, when controlling paper thickness, attention must be paid to changes in pulping degree to avoid over-refining, which may negatively impact the user experience.
10. Paper Wrinkling and Formation Quality: Improving Paper Structure Through Pulping
Wrinkles in tissue paper are often related to the drying process, reflecting uneven distribution within the paper web. By reducing the pulping degree and improving the paper formation process, the structure distribution can be enhanced, thereby reducing wrinkles and improving the flatness and appearance of the paper.
11. Water Carryover and Pulping Adjustment
Excessive water carried into the finishing rolls can cause crushing of the finishing rolls. In this case, reducing the pulping degree and increasing the temperature of the pulp can help reduce water carryover, protecting the finishing rolls and ensuring a smooth paper surface.
12. Solving Curling Problems in Tissue Paper
Curling is a common issue in tissue paper production. By increasing the amount of short fibers or reducing the pulping degree, the curling problem can be effectively alleviated, maintaining the flatness of the paper.
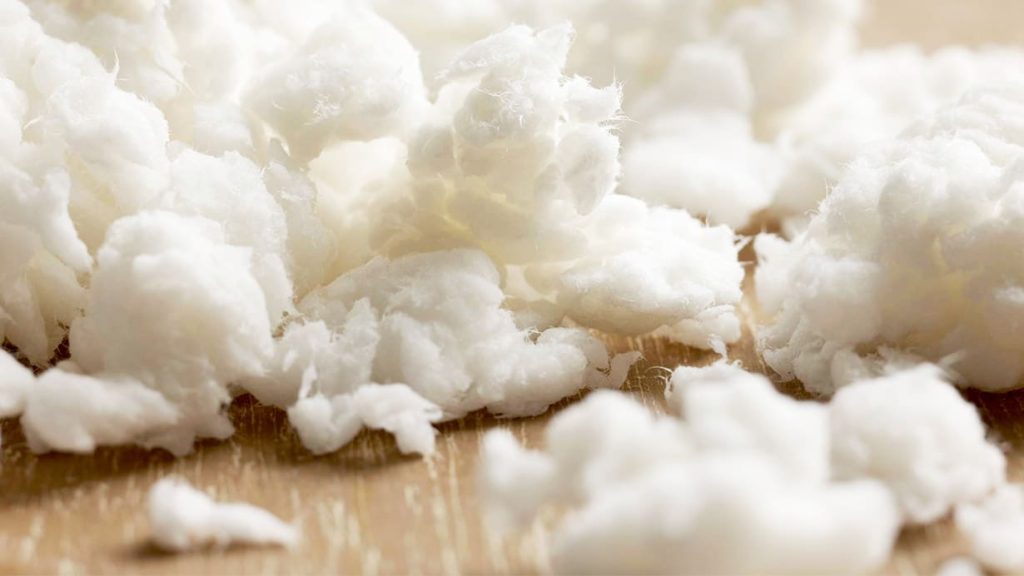
13. Permeability and Pulping
The porosity or permeability of paper changes rapidly with the pulping degree. Increasing the pulping degree and concentration can significantly increase the resistance to airflow, which positively impacts the production of tissue paper with strong absorbency.
14. Fiber Lifting and Pulping Degree
Fiber lifting on the surface of tissue paper is mainly caused by insufficient sizing or false sizing, and low pulping degree can exacerbate this problem. By appropriately increasing the pulping degree, the bonding strength between fibers can be enhanced, reducing fiber lifting and improving the smoothness and user experience of the paper.
15. Single-Sided Glazed Paper and Formation Issues
In the production of single-sided glazed tissue paper, if the surface quality is poor, it is often due to poor formation or insufficient adhesion of the sheet to the cylinder. Increasing the pulping degree can improve the uniform distribution of the pulp, enhancing both the paper’s formation and its adhesion to the cylinder.
16. Long Fiber Content and Formation: Optimizing Pulping Degree
When the paper’s formation quality is poor, it is often related to inadequate drainage in the wire section or excessive long fiber content. Increasing the pulping degree can help improve formation, but reducing the use of long fibers and optimizing pulping techniques are essential for achieving optimal results.
Conclusion
Pulping technology plays a crucial role in tissue paper production. By controlling the pulping degree, various performance indicators of the paper, such as strength, thickness, softness, and permeability, can be effectively adjusted. Mastering pulping techniques not only enhances product quality but also improves production efficiency, meeting the demands of different markets.