Why Does Tissue Mother Rolls Need the Slitting and Rewinding Process?
In the tissue paper industry, the production of high-quality tissue products begins with the creation of large tissue mother rolls. These massive rolls serve as the foundational material from which a wide range of tissue products—such as toilet paper, facial tissues, and paper napkins—are produced. However, before these products reach the consumer, the mother rolls must undergo a critical process: slitting and rewinding. This process, though often overlooked, plays a pivotal role in ensuring the final product meets the necessary standards of size, texture, and usability.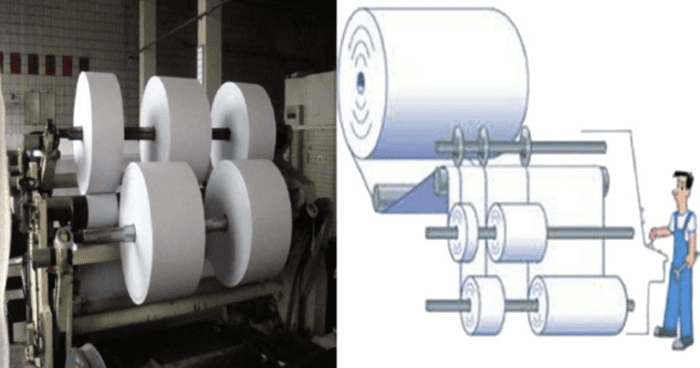
Understanding Tissue Mother Rolls
- What Are Tissue Mother Rolls?
- Characteristics of Tissue Mother Rolls
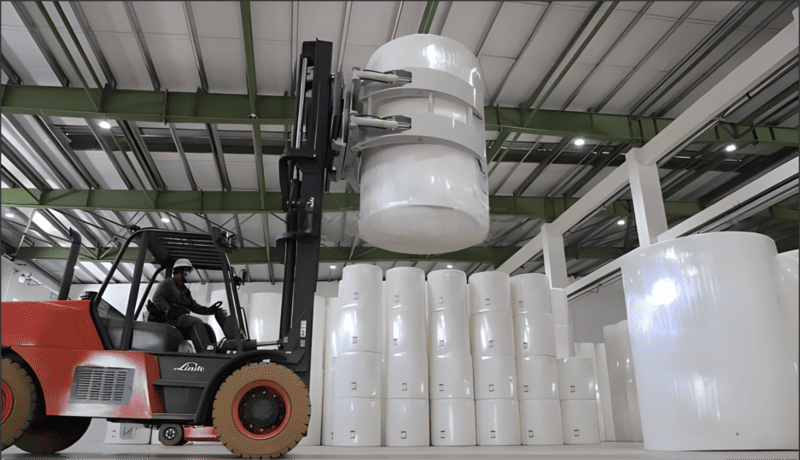
The Importance of the Slitting and Rewinding Process
- Why Slitting and Rewinding Is Necessary
- How the Process Enhances Product Quality
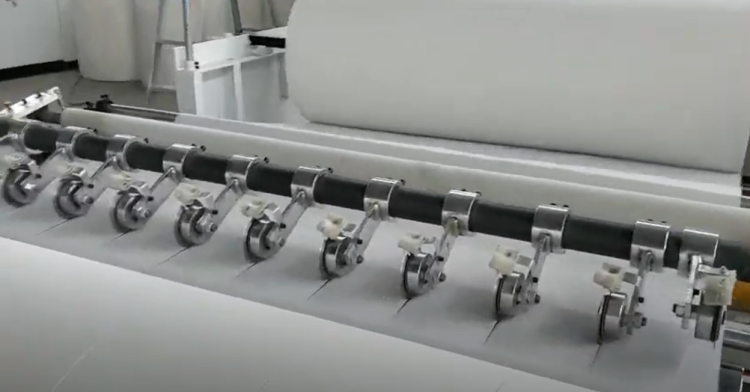
The Mechanics of Slitting and Rewinding
- How Slitting Machines Work
- The Role of Rewinding in the Process
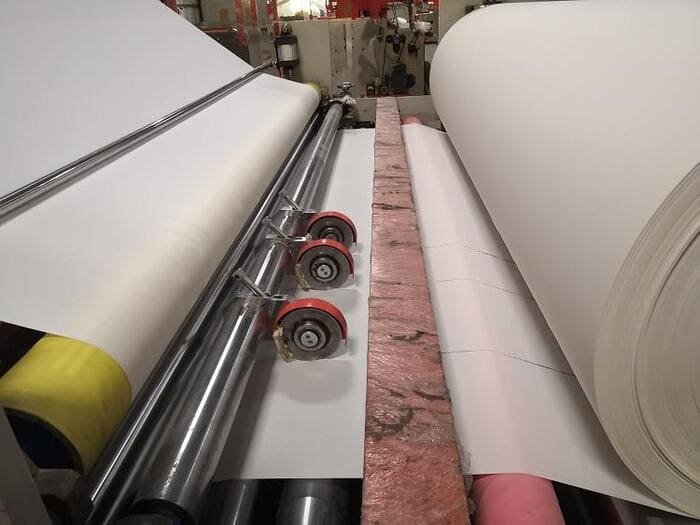
Types of Slitting and Rewinding Machines
- Different Machines for Different Products
- Manual vs. Automatic Machines
The Process Flow of Slitting and Rewinding
- Step-by-Step Overview
Common Challenges in Slitting and Rewinding
- Potential Issues During the Process
- Solutions and Best Practices
Technological Advances in Slitting and Rewinding
- Automation and Precision
- Real-Time Monitoring and Control
The Role of Slitting and Rewinding in Product Customization
- Meeting Specific Customer Requirements
- Enabling Private Label Production
Environmental Considerations in Slitting and Rewinding
- Reducing Waste
- Energy Efficiency
Safety Considerations in Slitting and Rewinding
- Ensuring Operator Safety
- Machine Safety Features
Quality Control in Slitting and Rewinding
- Maintaining Consistency
- Inspection and Testing
The Impact of Slitting and Rewinding on Production Efficiency
- Maximizing Throughput
- Reducing Downtime
Market Demand and Slitting and Rewinding
- Adapting to Changing Market Needs
- Scaling Production
Future Trends in Slitting and Rewinding
- Advancements in Machine Technology
- Sustainability Innovations
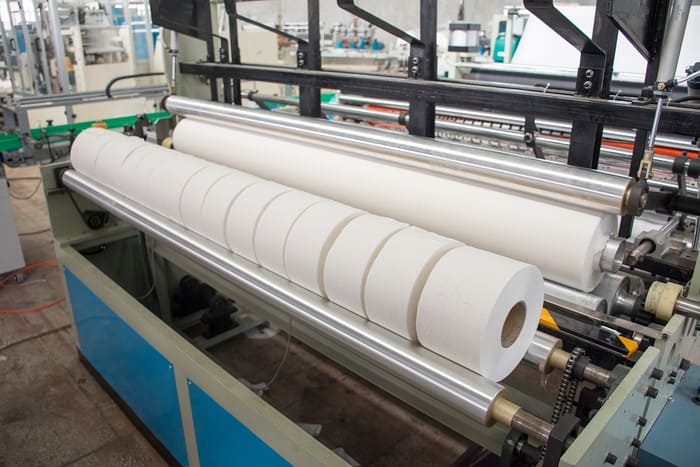
Conclusion
The slitting and rewinding process is a critical step in the tissue paper production industry, ensuring that large tissue jumbo rolls are transformed into the smaller, consumer-ready products that we use every day. This process not only determines the size and quality of the final product but also plays a significant role in maintaining production efficiency and sustainability. As technology continues to advance, the slitting and rewinding process will evolve, offering even greater precision, efficiency, and environmental benefits. For manufacturers, staying at the forefront of these advancements is key to producing high-quality tissue products that meet the ever-changing demands of the market.FAQ
1. What is the primary purpose of slitting and rewinding in tissue production?
The primary purpose of slitting and rewinding is to convert large tissue mother rolls into smaller, more manageable rolls that are ready for consumer use. This process ensures that the final products are the correct size and quality.
2. Can the slitting and rewinding process affect the quality of tissue products?
Yes, improper slitting and rewinding can lead to issues such as uneven rolls, tearing, and incorrect perforation, all of which can negatively impact the quality of the final product.
3. What types of slitting and rewinding machines are used in the tissue industry?
The tissue industry uses a variety of slitting and rewinding machines, including manual and automatic machines, each designed for specific types of tissue products.
4. How does automation improve the slitting and rewinding process?
Automation enhances the slitting and rewinding process by increasing precision, consistency, and speed. It also reduces the need for manual intervention, lowering the risk of errors and improving overall efficiency.
5. What role does quality control play in slitting and rewinding?
Quality control is essential for ensuring that each roll produced during the slitting and rewinding process meets the necessary standards for size, ply, and winding tightness. This helps maintain product consistency and quality.
6. How does the slitting and rewinding process contribute to sustainability in the tissue industry?
The slitting and rewinding process contributes to sustainability by optimizing material use, reducing waste, and using energy-efficient machinery, which minimizes the environmental impact of tissue production.