Why is Through-Air Drying (TAD) Technology Attractive to Tissue Paper Manufacturers?
Through-Air Drying (TAD) technology, abbreviated as TAD, was pioneered by Procter & Gamble in the mid-1960s for the production of hygiene paper products. Over half a century, world-renowned household paper producers and hygiene paper machine suppliers, including Procter & Gamble and Kimberly-Clark, have made a series of improvements and promoted the application of TAD technology. However, traditional TAD drying still faces issues such as high energy consumption, complex processes, and large capital requirements, especially the need for natural gas, leading to high energy consumption and costs for household paper producers, causing many paper mills to hesitate.
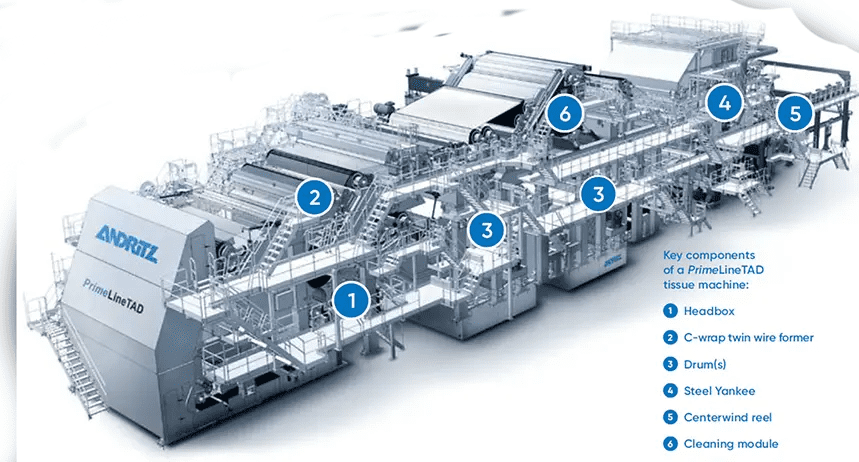
In recent years, some papermaking equipment companies in China have also conducted research and development, successfully producing ultra-high bulkiness hygiene paper base paper using a new type of steam energy-saving through-air drying paper machine that does not require natural gas.
While many components used in TAD are similar or identical to those in conventional drying, the TAD process in hygiene paper production differs significantly from regular drying. A typical TAD paper machine is much larger than a regular hygiene paper machine. It requires over twice the drying energy of a regular hygiene paper production line and more chemicals in the TAD process. Therefore, through-air drying requires more investment and operating costs. However, the improvement in paper performance and extremely high paper quality can offset this additional investment.
1. Improved Paper Quality
Improved paper performance is evident in the structural softness and surface softness of toilet paper. For tissue paper products, their absorbency is about twice that of regular paper. Both the bulkiness of toilet paper and tissue paper have been greatly improved. On the one hand, high-quality paper can command higher market prices. On the other hand, the improvement in paper performance lays the foundation for fiber savings, which is the potential for reducing the amount of fiber raw materials used. For example, 2-ply TAD tissue paper can replace 3-ply regular tissue paper, giving TAD an economic advantage. Although many components in a TAD paper machine are similar to those in a regular paper machine, special equipment is still needed to meet the special requirements for producing TAD paper.
A typical TAD paper machine has a twin-wire former with a multi-layer headbox (usually 3 layers), and now it is also equipped with a diluted water control system to achieve uniform cross-directional quantification distribution. The permeability of the paper varies with the increase in quantification. Any fluctuations in quantification can lead to uneven cross-directional distribution, which is exacerbated during the TAD drying process. Therefore, uniform cross-directional quantification distribution is crucial for obtaining high-quality paper and maintaining stable paper machine performance. The forming rolls can be regular rolls or vacuum rolls. Vacuum rolls are used for the two-sided dewatering of high-quantification paper and high-speed paper machines, which can improve the production efficiency of the paper machine.
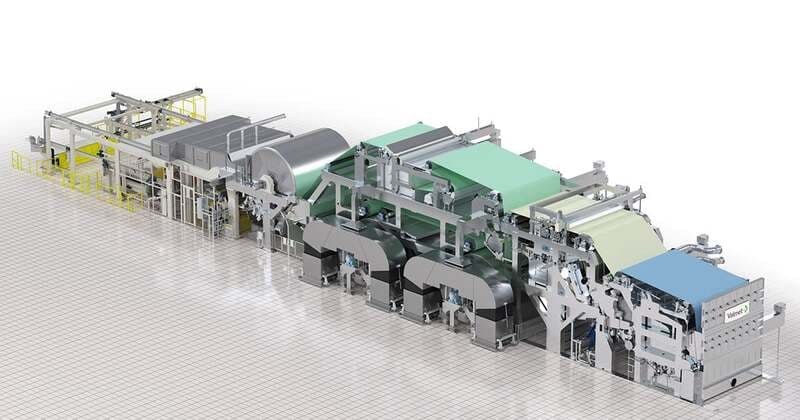
2. No Pressing
One of the differences between a TAD paper machine and a regular hygiene paper machine is the absence of mechanical pressing. The paper web is not compressed, so the bulkiness and free volume inside the paper are not compromised, resulting in higher absorbency. The paper web is dehydrated to a dryness of about 25% using only vacuum, but this requires a lot of electricity. The vacuum boxes operate within the inner wire, and generally, the steam boxes installed above the vacuum boxes can enhance dehydration. Additionally, it is the only device in the entire production process that affects the transverse distribution of moisture.
After vacuum dehydration, the paper web is transferred to a TAD drying fabric, usually with a three-dimensional structure. A forming box behind the vacuum dehydrator draws the paper web onto the TAD drying fabric. At this point, the TAD paper web acquires its typical three-dimensional structure and remains unpressed.
The next step is the hot drying of the dehydrated paper web. On a TAD paper machine, the dryness of the dehydrated paper web is 25%-27%, compared to 38%-42% for a general paper machine. This means that TAD requires almost twice as much energy to remove moisture as conventional drying, resulting in higher energy consumption.
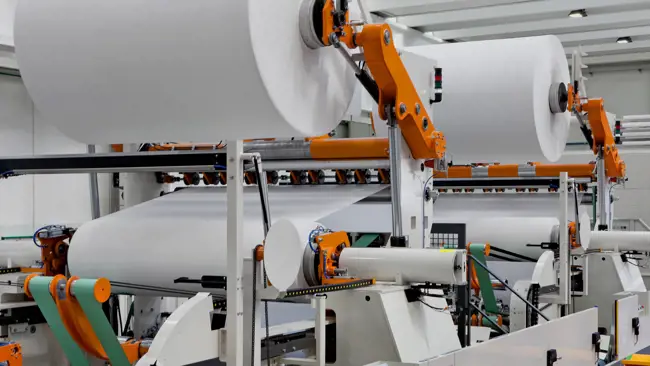
3. Several TAD Design Options
Different suppliers offer different designs for the TAD drying section. For example, Andritz offers a design consisting of a large, penetrable cylinder with a hot air hood. The hot air blown by the hot air hood passes through the paper web and is sucked into the cylinder. The latest TAD cylinder and hot air system have been developed to meet the following system requirements: an unlimited service life for the cylinder structure and a very uniform distribution of hot air temperature and speed at the hot air hood outlet. The TAD hot air system is large, with a hot air volume about four times that of a conventional Yankee hood. The blowing temperature is 200-250°C, much lower than the temperature in a regular hygiene paper machine’s hood. Special mixers and grates can evenly adjust the distribution of temperature and speed, and the use of computational fluid dynamics (CFD) algorithms helps optimize the entire hot air system.
Other TAD drying section designs include medium-sized twin TAD cylinders with two independent hot air hoods (Cole patent from 1969). According to the Sission patent from 1967, drying hot air is blown out of the cylinder, passes through the paper web, and is then blown into the hot air hood. This method uses three small cylinders. Depending on the selected drying process design, the dryness of the paper web after passing through the TAD drying section can vary between about 50% and 70%-80%. A Yankee dryer is used for the final drying and creping of the paper web. Another special TAD design is used to dry the paper web to a final dryness of only 96%-98% in the TAD drying section. In this case, the creping of the paper web is completed at different wire speeds in the wet section. Kimberly-Clark holds the patent for this technology, known as Uncreped Through-Air Drying (UCTAD).
After the TAD drying section, a regular reel places the paper web onto the Yankee dryer, and then the paper web passes through the Yankee dryer and hot air hood. Except for the lack of a cross-directional adjustment system in the hot air hood, the Yankee dryer and hot air hood in this process are not significantly different from those used in a regular hygiene paper machine. However, only special chemicals can adhere the TAD paper web with its three-dimensional knuckle and pillow structure to the Yankee dryer, as the paper web does not naturally adhere to the Yankee dryer at higher dryness levels. After creping, the TAD paper web has its typical structure and fine creases.
4. Differences Caused by TAD Drying
Unlike a regular paper machine, a calender is part of the through-air drying process. The calender can adjust the thickness of the paper web and improve its surface softness. Another important issue is the control of the paper web between the creping blade and the reel, as the soft TAD paper web is more prone to flutter than regular hygiene paper. Several special control devices have been developed, such as active guide blades and guide blades at the entry of the cal
ender and reel. Efficient lint removal devices are essential in the drying section because a considerable amount of lint is produced during the through-air drying process.
Finally, a reel with an auxiliary drive for axis winding applies low pressure to the pressure zone between the large-diameter paper roll and the reel cylinder, helping maintain the paper’s high bulkiness. Additionally, it can be used for winding large-diameter rolls of paper. Andritz’s solution is to use force sensors to control the pressure in the pressure zone and maintain low pressure throughout the entire reeling process to avoid reducing the bulkiness.
Although many components of a TAD paper machine are similar to those of a regular paper machine, some special equipment is still needed to meet the high-quality requirements for TAD hygiene paper. Despite some drawbacks in the relatively complex TAD process, the exceptional quality and performance of the paper economically interest hygiene paper producers in adopting TAD for paper production.
If you have a need for purchasing TAD tissue paper parent roll, please contact Yuanhua Paper, and we will offer you the most affordable factory price!
People also ask?
- What is through air drying
- What is the process of air drying?
- What is a tad tissue machine?
- What is air dry?