What is Tissue Paper Jumbo Roll Converting?
Tissue paper is a soft, absorbent, and disposable paper product that has various uses in personal hygiene, household cleaning, food service, and industrial applications. Tissue paper products include facial tissues, paper towels, napkins, toilet paper, and others.
Tissue paper production involves making large rolls of tissue raw material, called jumbo rolls, from raw materials such as wood pulp or recycled paper. These tissue jumbo rolls are then converted into smaller tissue rolls or folded products that are ready for the market. This process is known as tissue paper jumbo roll converting.
Below, we will explain what tissue paper jumbo roll converting is, why it is important for the tissue paper industry, how it is done, and what are some of the matters needing attention in this process.
What is the Converting Production of Tissue Paper Jumbo Roll?
Definition of Tissue Jumbo Roll Converting
Tissue paper jumbo reel converting is the process of transforming jumbo rolls of tissue raw material into finished tissue paper products. Converting involves several steps such as unwinding, cutting, embossing, rewinding, and packaging.
- Unwinding is the process of feeding the jumbo roll into the converting machine.
- Cutting is the process of slicing the jumbo roll into smaller widths or lengths according to the desired product size.
- Embossing is the process of creating patterns or designs on the tissue surface to enhance its appearance, softness, strength, and absorbency.
- Rewinding is the process of winding the cut and embossed tissue into smaller rolls or folds.
- Packaging is the process of wrapping and labeling the final products for distribution.
Importance of Jumbo Roll Converting in the Tissue Paper Industry
Jumbo roll converting is an essential part of the tissue paper industry because it allows forefficient and cost-effective production of various tissue paper products. By using jumbo rolls,tissue paper manufacturers can reduce waste, save energy, and optimize storage and transportation space.
Jumbo roll converting also contributes to the quality and consistency of the final tissue paper products. By using advanced machinery and technology, tissue paper converters can ensure precise cutting, uniform embossing, smooth rewinding, and secure packaging of the products. Moreover, tissue paper converters can add value to the products by offering customized options such as different colors, prints, fragrances, or additives.
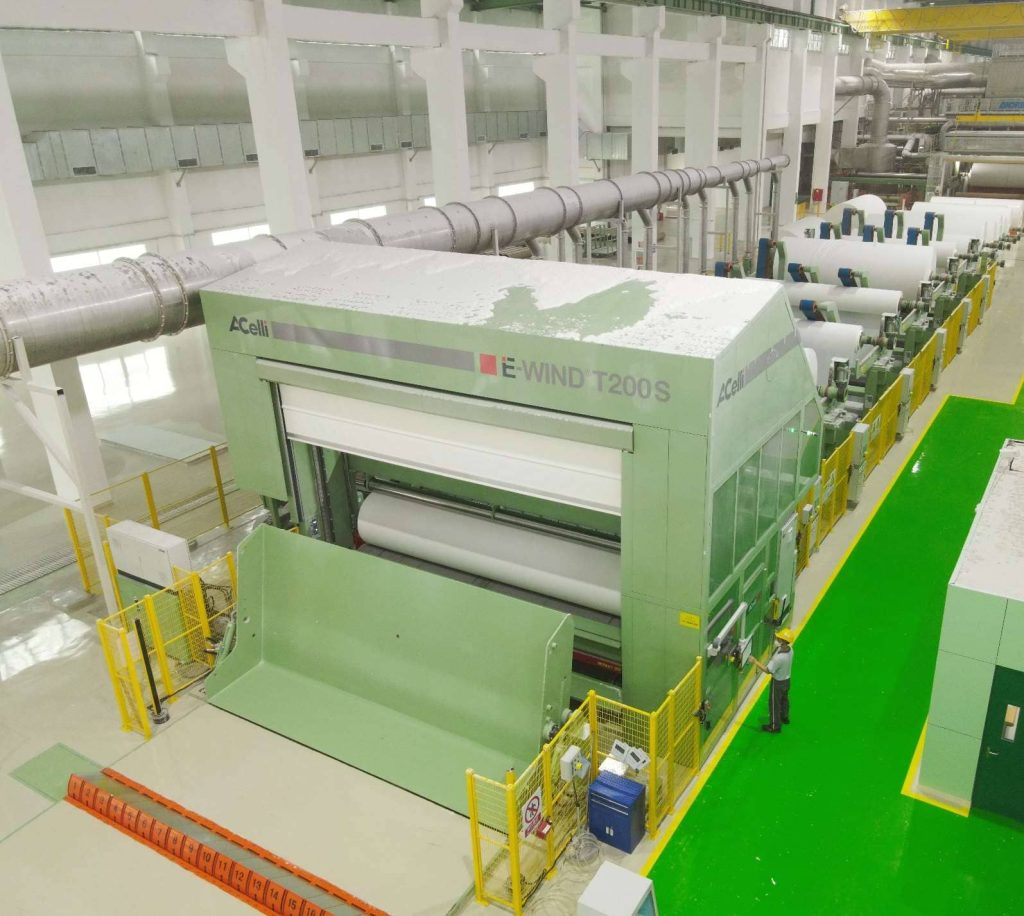
What is The Converting Process of Tissue Paper Parent Roll?
The Production of Tissue Jumbo Rolls
The production of jumbo rolls starts with preparing the raw materials for tissue paper making. These raw materials can be either virgin wood pulp or recycled paper. Virgin woodpulp is obtained from trees that are harvested and processed into wood chips. Recycled paper is collected from various sources such as offices, households, or industrial waste.
The raw materials are then pulped and refined to form a homogeneous slurry of fibers andwater. The slurry is then screened and cleaned to remove any impurities or contaminants.The slurry is then diluted and sprayed onto a moving wire mesh to form a thin layer of wettissue web.
The wet tissue web is then dried by passing through heated cylinders or air blowers. Thedried tissue web is then creped by scraping it off the cylinder with a blade. Creping creates micro-folds on the tissue surface that increase its softness, bulkiness, and stretch ability.
The creped tissue web is then wound onto large reels that cover the full width of the tissue machine. These reels are called jumbo rolls or parent rolls. A jumbo roll can weigh up to several tons and have a diameter of up to 3 meters.
The Converting Process: From Jumbo Roll to Final Product
The converting process involves cutting the tissue mother roll into smaller rolls or folds using developed, high-tech and high-speed types of machinery. The quality of the machinery plays an important role in the winding, cutting, slitting, printing and embossing steps of the converting.
- The first step in the converting process is unwinding. The jumbo roll is fed into an unwinder that controls its tension and speed. The unwinder also has sensors that detect any defects or breaks in the tissue material.
- The second step is cutting. The unwound tissue web is cut into smaller widths or lengths according to the desired product size. For example, a jumbo roll can be cut into several narrow rolls for toilet paper or facial tissues; or into several long sheets for napkins or papertowels.
- The third step is embossing. The cut tissue web is passed through two rollers that haveengraved patterns or designs on their surfaces. The rollers press against each other andimprint their patterns on the tissue surface. Embossing enhances the appearance, softness,strength, and absorbency of the tissue paper.
- The fourth step is rewinding. The embossed tissue web is wound onto smaller cores or folded into stacks. The rewinder also controls the tightness and diameter of the rolls or folds. The rewinder can also add glue or perforations to the tissue web to facilitate tearing or separating the products.
- The fifth step is packaging. The rewound or folded tissue products are wrapped and labeledwith plastic film or paper. The packaging machine also counts and sorts the products into bundles or boxes for distribution.
Machinery Involved in the Converting Process
The machinery and technology used in the converting process vary depending on the typeand size of the tissue paper products. Some of the common types of machinery are:
- Unwinders: These are machines that feed the jumbo roll into the converting machine.They have brakes, clamps, and sensors that control the tension and speed of the jumboroll.
- Cutters: These are machines that slice the tissue web into smaller widths or lengths.They have knives, blades, or saws that cut the tissue web with precision and accuracy.
- Embossers: These are machines that create patterns or designs on the tissue surface.They have rollers that have engraved patterns or designs on their surfaces. They canalso apply glue, lotion, fragrance, or additives to the tissue web.
- Rewinders: These are machines that wind the cut and embossed tissue web ontosmaller cores or folds. They have shafts, belts, and sensors that control the tightnessand diameter of the rolls or folds. They can also add glue or perforations to the tissueweb.
- Packers: These are machines that wrap and label the final tissue products. They havefilm or paper dispensers, sealers, and printers that wrap and label the products withspeed and efficiency. They can also count and sort the products into bundles or boxes.
Matters Needing Attention in Tissue Paper Mother Roll Converting
Quality Control
Quality control is an important aspect of tissue paper base roll converting because itensures that the final products meet the standards and expectations of the customers.Quality control involves maintaining high standards of quality throughout the convertingprocess, from raw materials to finished products.
Some of the steps taken to ensure quality are:
Regular machinery maintenance: This involves checking, cleaning, repairing, andreplacing any parts or components of the converting machinery that may affect itsperformance or cause defects in the products.
Monitoring of raw materials: This involves inspecting and testing the raw materials suchas wood pulp or recycled paper for their quality, consistency, and suitability for tissue paper making.
Product testing: This involves testing the final products for their physical and functional properties such as thickness, weight, strength, softness, absorbency, brightness, color, printability, etc.
Safety Measures
Safety measures are another important aspect of tissue semi material big roll converting becausethey prevent accidents and injuries in the converting process. Safety measures involve identifying and eliminating any potential hazards in the converting process, such as fire, electricity, noise, dust, chemicals, etc.
Some of the safety protocols and measures taken are:
- Fire prevention: This involves installing fire detectors, extinguishers, sprinklers, andalarms in the converting area. It also involves avoiding any sources of ignition such assparks, flames, cigarettes, etc.
- Electrical safety: This involves using proper wiring, grounding, insulation, and protectionfor all electrical equipment and devices in the converting area. It also involves avoidingany contact with live wires or exposed terminals.
- Noise reduction: This involves using noise-reducing materials such as rubber mats,foam pads, or acoustic panels in the converting area. It also involves wearing ear plugsor muffs when working near loud machinery.
- Dust control: This involves using dust collectors, filters, vacuums, or fans to remove anydust particles from the air in the converting area. It also involves wearing masks orrespirators when handling dusty materials.
- Chemical safety: This involves using proper storage, handling, labeling, and disposal ofany chemicals used in the converting process such as glue, lotion, fragrance, additives,etc. It also involves wearing gloves, goggles, aprons, or suits when working withchemicals.
Environmental Considerations
Environmental considerations are another important aspect of tissue paper master roll converting because they address the environmental implications of tissue paper production such as waste management and energy consumption.
Some of the strategies for minimizing environmental impact are:
- Recycling: This involves reusing or reprocessing any waste materials generated in theconverting process such as trimmings, cores, wrappers, etc. Recycling reduces waste disposal costs and saves natural resources.
- Energy efficiency: This involves using energy-efficient machinery and technology in the converting process such as variable speed drives (VSDs), LED lights (LEDs), heat recovery systems (HRSs), etc. Energy efficiency reduces energy consumption costs and greenhouse gas emissions.
- Water conservation: This involves using water-efficient machinery and technology inthe converting process such as closed-loop systems, reverse osmosis (RO), membranefiltration (MF), etc. Water conservation reduces water consumption costs and waterpollution.
Over all, Tissue jumbo roll converting is the process of transforming jumbo rolls of tissue semi material big roll into finished tissue paper products. It is an essential part of the tissue paper industry because it allows for efficient and cost-effective production of various tissue paper products. It also contributes to the quality and consistency of the final tissue paper products.
Tissue paper jumbo roll converting involves several steps such as unwinding, cutting, embossing, rewinding, and packaging. It also involves using advanced machinery andtechnology that can perform these steps with precision and accuracy.
Tissue converting requires attention to quality control, safety measures, and environmental considerations. These aspects ensure that the final products meet the standards and expectations of the customers, prevent accidents and injuries in the tissue converting process, and minimize the environmental impact of tissue paper production.
By understanding what tissue paper jumbo roll converting is, how it is done, and what are some of the matters needing attention in this process, tissue paper manufacturers and converters can achieve successful and responsible converting operations.